
OEM Service Process
Requirement Communication
– Understanding Your Brand
We start by learning about your brand story, positioning, and design tone. This ensures our production fully supports your brand’s long-term strategy and values.
– Identifying Target Market Needs
We analyze your end market-whether commercial, residential, or specialized sectors-to align product design and standards with regional expectations.
– Clarifying Product Specifications
We collect detailed requirements on materials, dimensions, finishes, structure, and packaging to minimize rework and ensure precise execution.
– Confirming Lead Time & Quantity
We define the expected delivery timeline, minimum order quantity (MOQ), and batch size to ensure our production plan matches your supply chain needs.
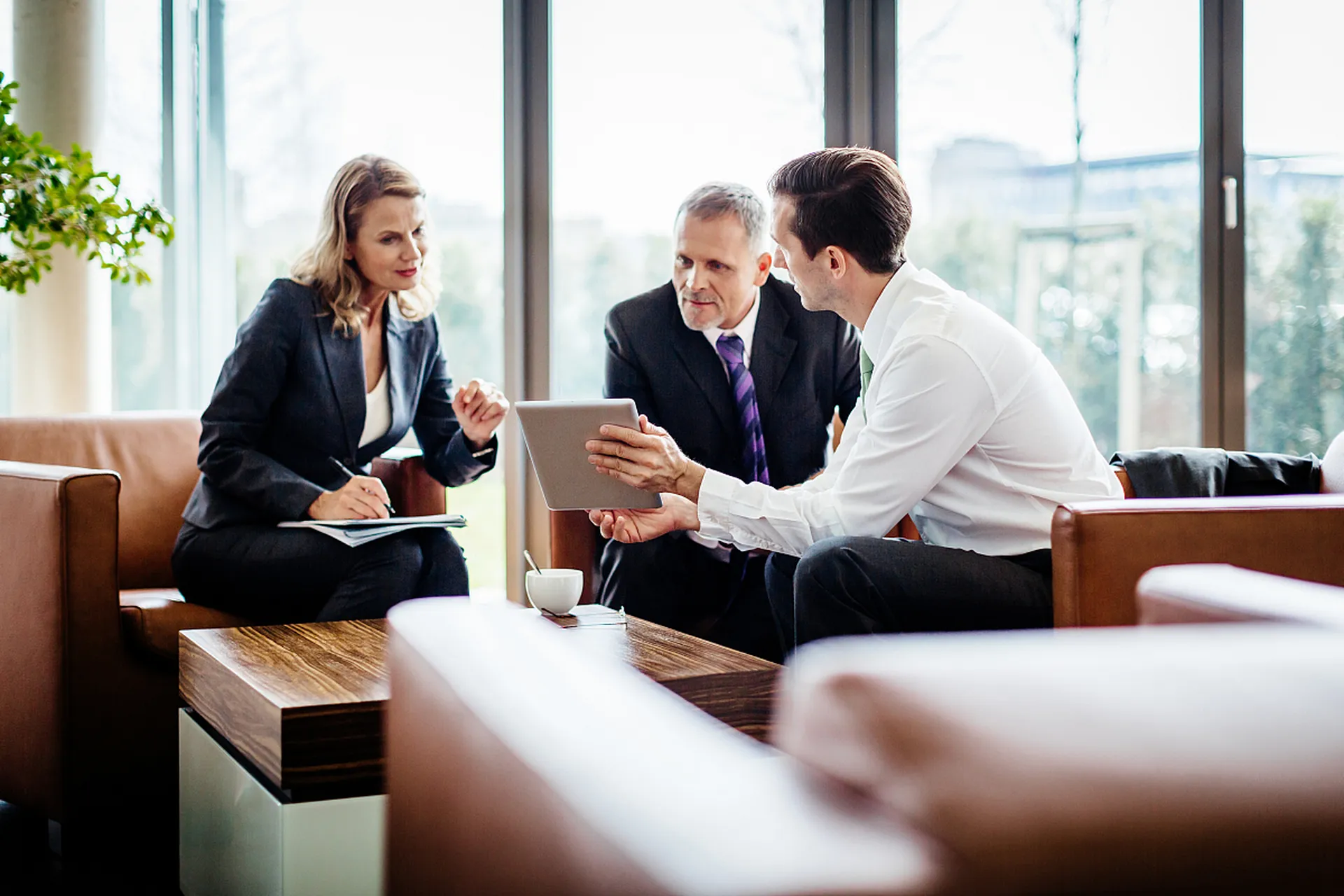
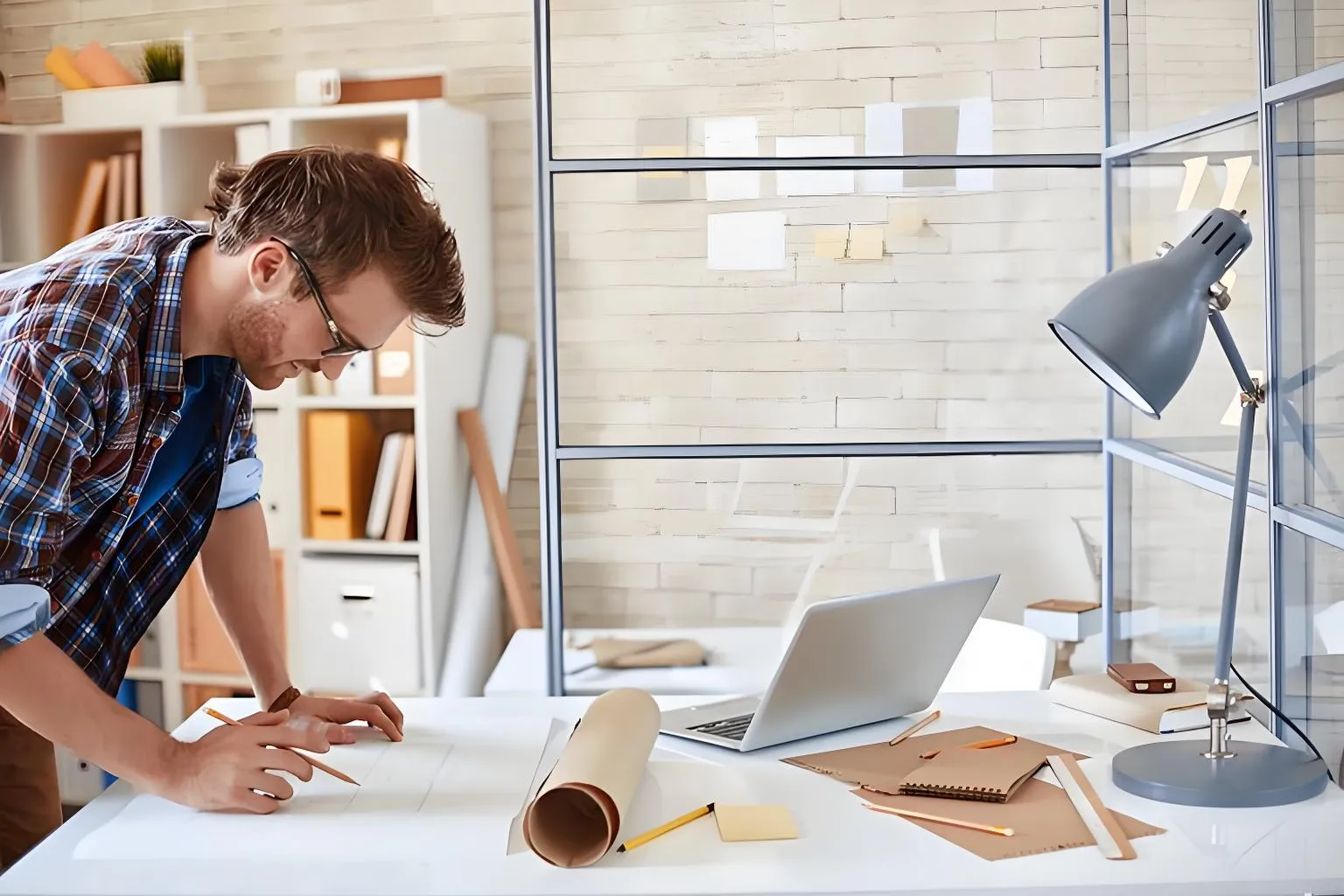
OEM Execution
– Reviewing Design Files or Samples
We examine the drawings, samples, or references you provide and confirm technical feasibility based on our production capability.
– Optimizing Structure & Materials
Our engineering team evaluates structural integrity and suggests material alternatives for cost-efficiency and durability.
– Quotation & Term Confirmation
We offer transparent pricing based on your specs, quantity, and trade terms (e.g., FOB, CIF, DDP), and confirm payment, production, and shipping terms.
– Prototype Approval
Before mass production, we create a sample or prototype to validate materials, construction, and finish. Your approval ensures confidence in final output.
Mass Production & Quality Control
– Material Sourcing & Pre-Production Check
We begin by sourcing materials from certified suppliers and conducting pre-production inspections to ensure consistency from the start.
– In Process Quality Monitoring
During production, we carry out multiple in-line inspections to catch and correct any issues before the final product stage. Our team also provides weekly progress updates, keeping you informed on key milestones, current status, and any potential risks – ensuring full transparency throughout the production process.
– Final Quality Check
All finished products undergo strict final inspections based on your AQL level or specific standards, including packaging checks.
– Third Party Testing & Reports
If required, we coordinate third-party inspections (e.g., SGS, TÜV) and provide test reports, certifications, or compliance documentation.
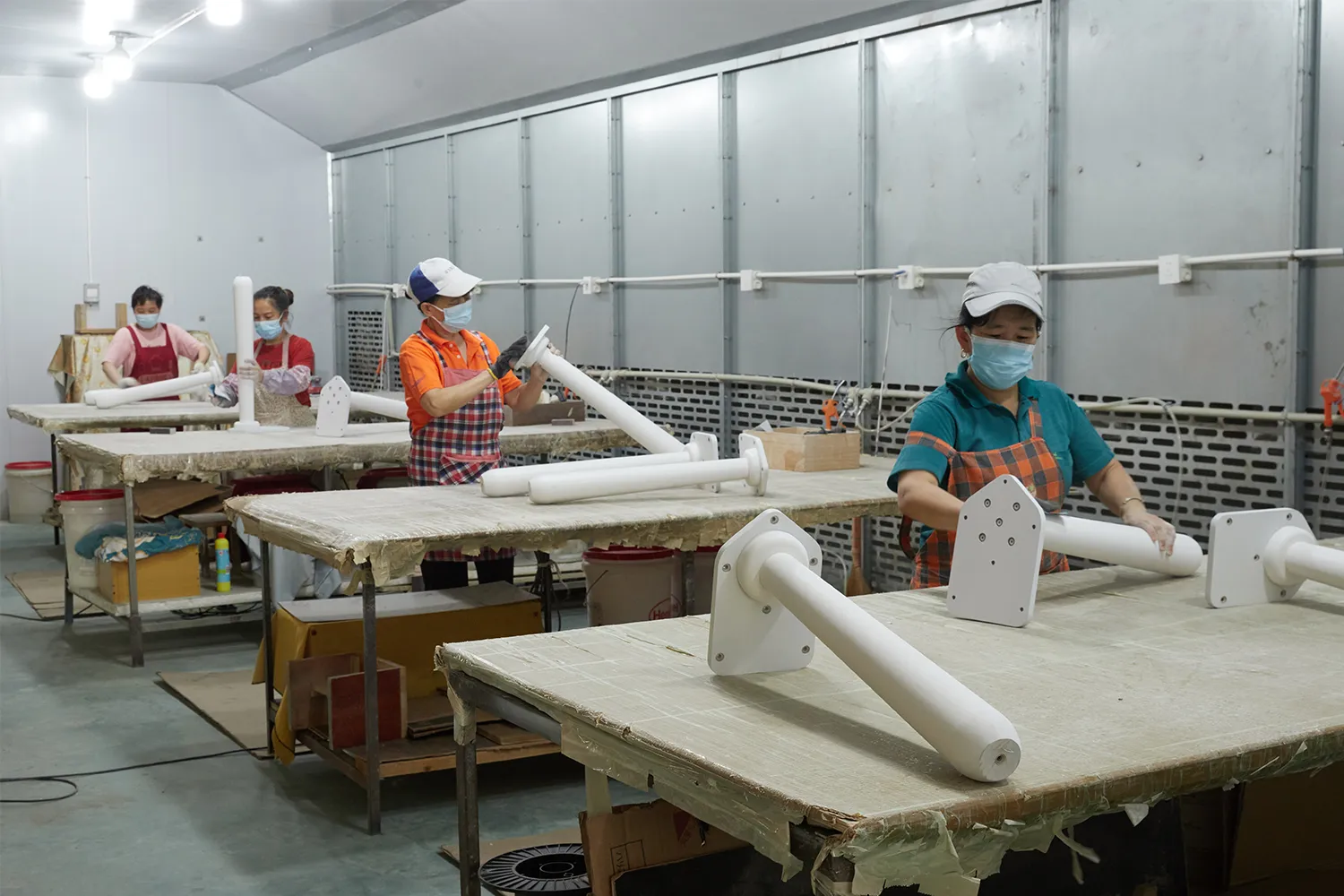
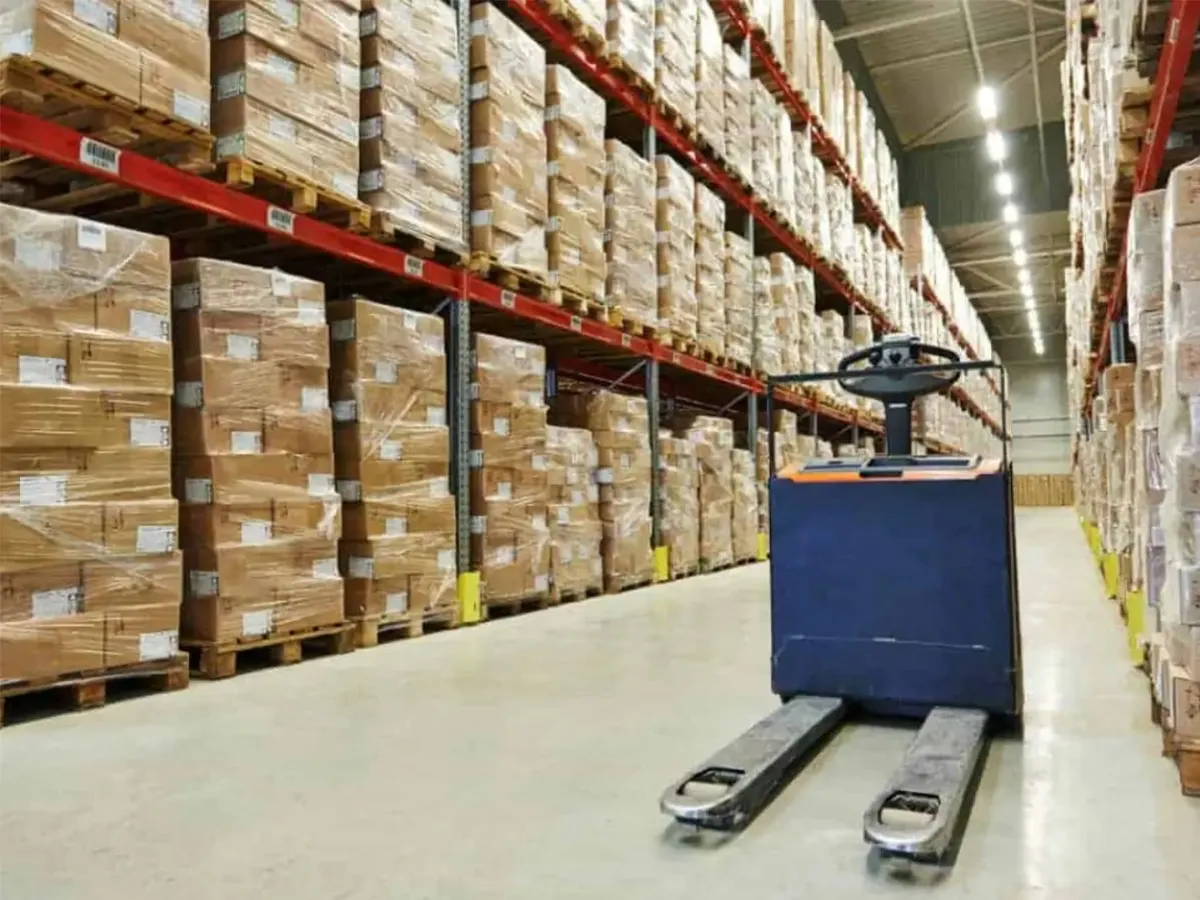
Logistics & Delivery
– Global Warehousing Network
We operate overseas warehouses in key markets including the USA, Canada, Japan, the UK, and several EU countries. This allows us to offer faster local delivery, reduce shipping costs, and support flexible inventory solutions for regional projects.
– Trade Term Flexibility
We support multiple Incoterms (FOB, CIF, DDP) to match your logistics setup, including support for overseas warehouse delivery if needed.
– Secure Packaging Solutions
All products are packed with care using protective materials, corner guards, and moisture-resistant packaging to avoid damage in transit.
– Global Freight Management
We partner with international logistics providers to offer sea, air, rail, or multimodal shipping with real-time tracking and customs clearance support.
– On Time Delivery Assurance
Each shipment is scheduled and tracked to ensure punctual delivery. You’ ll receive clear ETAs, shipping documents, and status updates throughout.
After-Sales Service
– Dedicated Account Management
You’ ll have a dedicated account manager who provides fast response, order follow-up, and communication throughout and after production.
– Reorder & Forecast Support
We assist with reorder planning and inventory forecasting based on your sales data and project pipeline to ensure steady supply.
– Long-Term Service Commitment
We aim to build lasting partnerships. Our team is ready to support your future projects, product upgrades, and growing business needs.
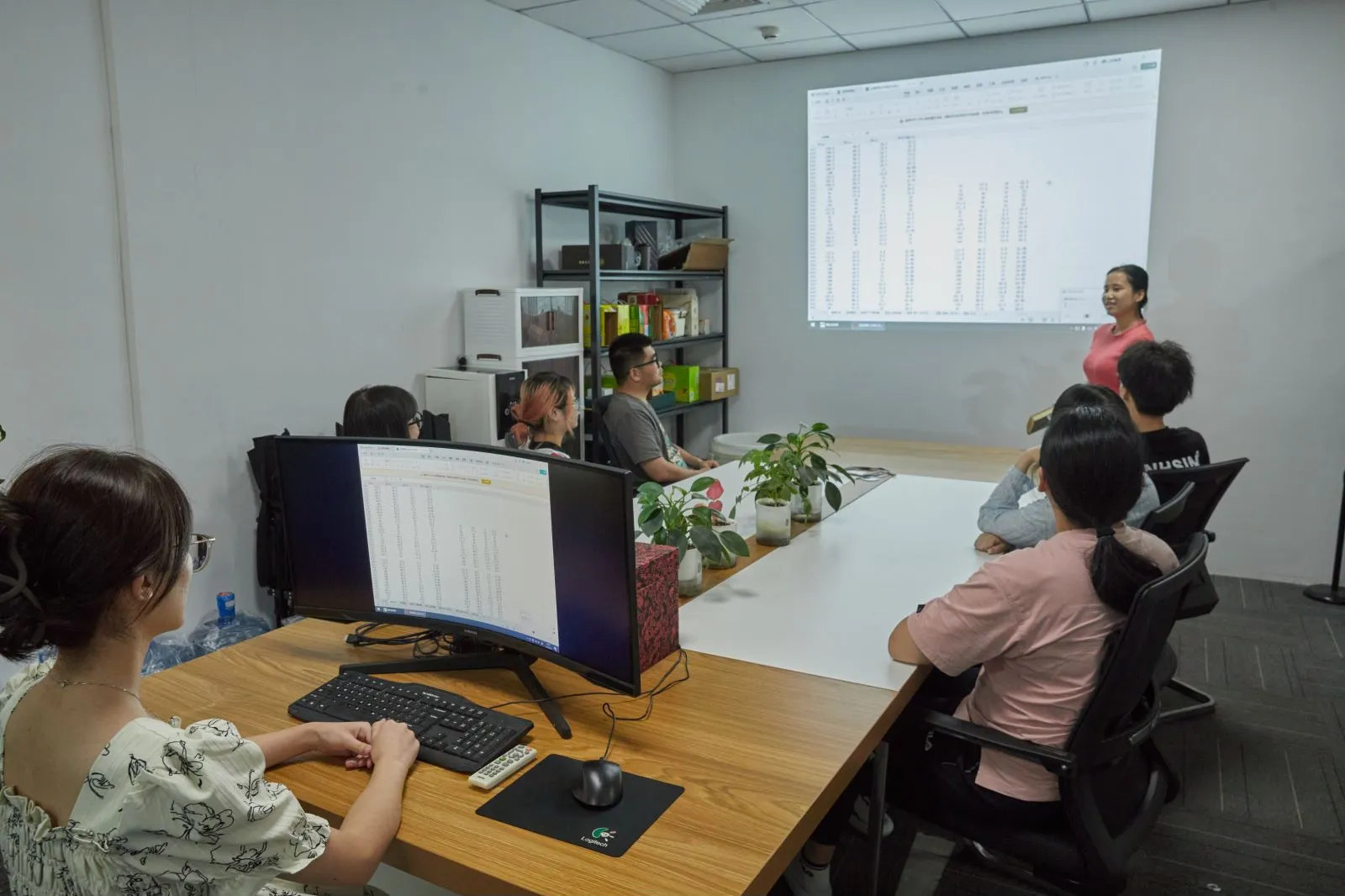